Immerse yourself in the fascinating world of toy design as we embark on an exploration into the captivating journey of Barbie’s evolution from inception to the present day. With the new Barbie movie showing in theaters worldwide, Design Engine wanted to show her some love. We’re not just talking about a doll here; we’re exploring the evolution of design, the nuances of ideation, material selection, and manufacturing that make Barbie such a noteworthy case study.
The History of Barbie
When Barbie first arrived in 1959, she was a fashion-forward, teenage fashion model. Barbie’s initial design was centered around a semi-adult figure, rather contrary to the baby dolls popular at the time. She represented a shift in toy industry ideation, a step into aspirational play, which enabled children to imagine the futures they could inhabit.
Over the decades, Barbie has become an icon for both children and adults around the world. She embodies a spectrum of cultures and evokes a sense of fascination with her design. Born from the vision of Ruth Handler, an American businesswoman, Barbie has experienced various changes over the years, transforming from a simple plastic doll into a symbol of limitless possibilities for children worldwide. From the perspective of toy product design, the evolution of Barbie is a testament to the power of innovation, technology, and adaptability.
Modern Barbie models are not only aesthetically more diverse but also uphold a more inclusive view of beauty. Recent additions include dolls with a range of body types, skin tones, and abilities. This move towards inclusivity isn’t just about social responsibility—it also represents a shift in ideation, hinging on the understanding of the diverse customer base.
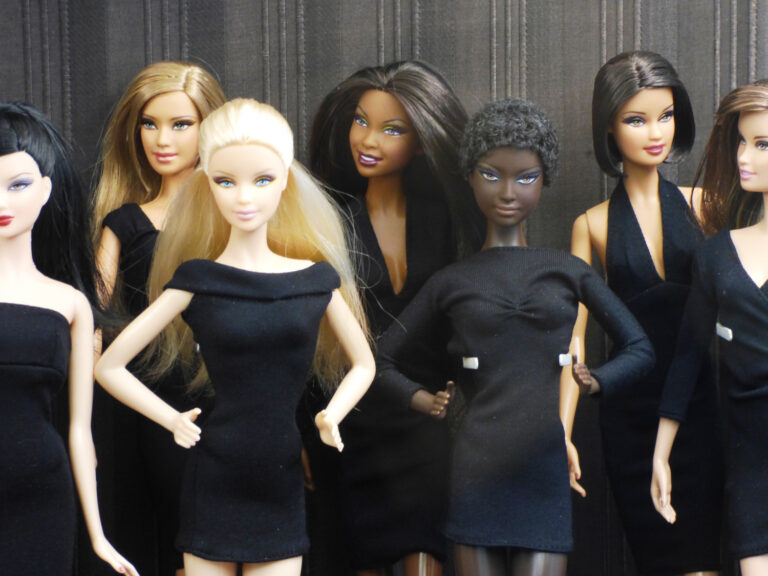
Photo by Tomasz Mikołajczyk from Pixabay
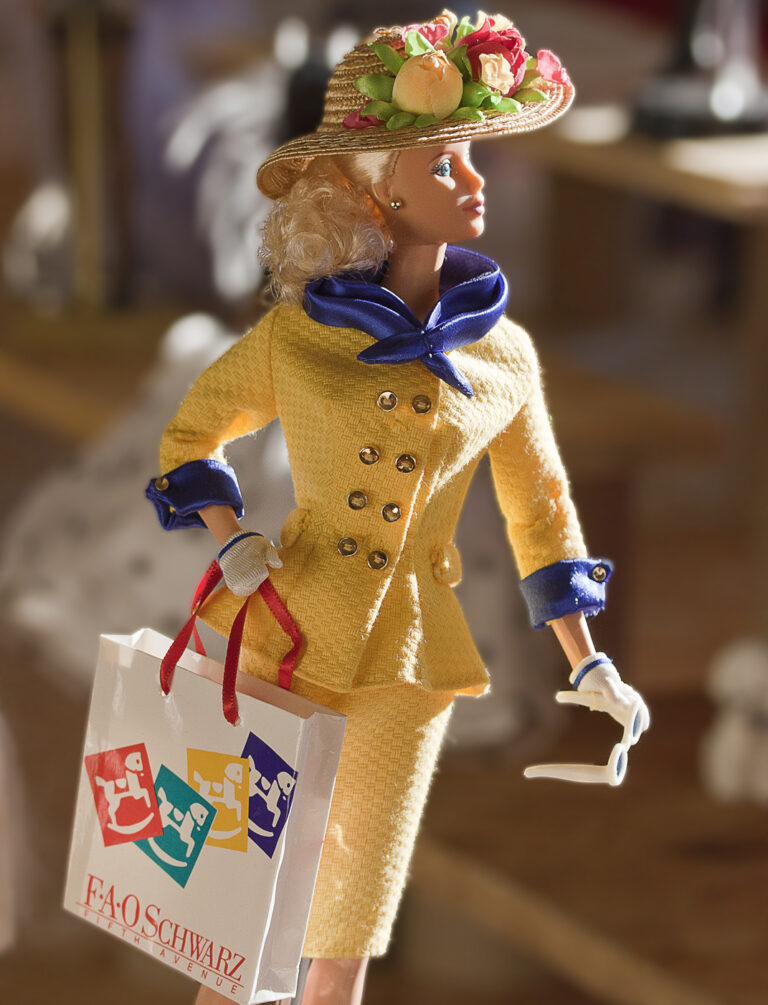
Photo by OrMaVaredo from Pixabay
The Material Evolution of Barbie’s Toy Design
Material selection played a critical role in Barbie’s design. In its early years, Barbie was primarily made of PVC (Polyvinyl Chloride). This allowed for more detail and a more realistic aesthetic than the hard plastic commonly used in dolls of that era. This also enabled the Barbie brand to incorporate a wide range of trendy fashions.
Manufacturing has always been a key aspect of Barbie’s evolution. In the early days, the process involved creating molds for the dolls and their accessories. Over time, Mattel introduced more variations, demanding more intricate molds and diverse manufacturing processes. Challenges included scaling production to meet global demand and adapting to changing safety regulations.
Changing environmental laws in Europe during the 1980s necessitated a significant shift in the doll’s material composition. PVC, when incinerated, produces hydrochloric acid, contributing to acid rain. This prompted Mattel, the company behind Barbie, to switch to more recyclable plastics or safer formulations of PVC.
Today, Barbie’s construction involves several types of plastics: a hard vinyl compound for the head, EVA (ethylene-vinyl acetate) for the arms, acetal for the torso covered by an elastomer, and PVC for the legs. The chosen materials give Barbie the durability, flexibility, and accessibility required in modern toy designs.
Role of 3D Software in Barbie's Toy Design
Let’s fast forward to the 21st century. Barbie’s design has become even more complex, partly due to technological advancements and the use of 3D design software. Such software allows designers to visualize the product in 3D, test different materials, and even simulate how the product will behave in real-world scenarios. It has revolutionized Barbie’s design process, allowing for unprecedented levels of detail and realism, as well as efficient iteration of designs.
The rise of 3D software, such as SolidWorks, has played a vital role in Barbie’s design evolution. These technological advancements have allowed designers to create intricate designs with precision and accuracy, significantly enhancing the final product’s quality. This ability to visualize, prototype, and validate designs digitally has made 3D software an essential tool in modern toy design.
SolidWorks, for example, enables designers to create realistic models and simulate the real-world performance of their designs. As a result, the software allows for a faster, more efficient design process, helping Mattel and other toy manufacturers adapt to changing market demands and maintain a competitive edge.
Are You Interested in a Toy Design Career?
Barbie’s journey illustrates how technological advancements and societal shifts have influenced toy product design. This evolution highlights the importance of flexibility, innovation, and understanding the target market in product design. Furthermore, it underscores the role of modern tools like SolidWorks in shaping the future of product design.
As a designer or engineer looking to venture into toy design, gaining proficiency in SolidWorks can be a game-changer. SolidWorks training not only equips you with the skills to design high-quality products but also provides you with an understanding of how to adapt to market trends and customer demands.
So, what’s the takeaway for you, an aspiring or seasoned product designer? First off, understand that great design is evolutionary. It doesn’t just meet the demands of the present—it anticipates the needs and wants of the future. Second, it’s crucial to leverage the latest design tools, like SolidWorks and Creo, to bring your vision to life in this dynamic, competitive market.
Design Engine offers a wide array of training classes tailored to help you harness your design skills. By leveraging these classes, you can gain a deeper understanding of the toy design process and take your product design skills to the next level.
* The featured image was taken by ErikaWittlieb from Pixabay. *
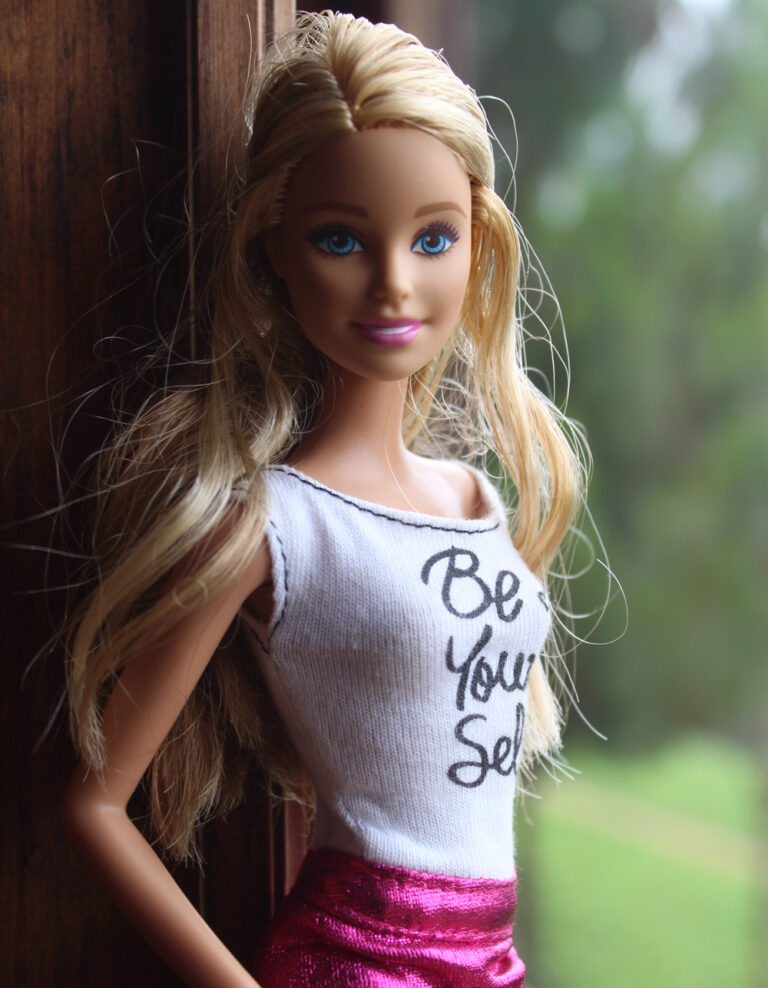
Photo by Sandra Gabriel on Unsplash